【导读】据麦姆斯咨询报道,几乎所有的汽油车都是由发动机控制模块(engine control module,ECM)与传感器和执行器一起组成发动机控制系统。该系统最关键的输入把控则是歧管绝对压力(MAP)传感器。在“速度密度式”状态下,MAP传感器能够侦测发动机中流动的空气情况,从而确定喷油时间和提前点火时间以实现最佳运行。
即使是依靠对进气量进行直接测量的车辆也需要配备大气绝对压力(BAP)传感器,主要用于高气压测量补偿。如今生产商每年都生产数以千万计的MAP和BAP传感器,过去十年里推动了几代压力传感器模组的设计。
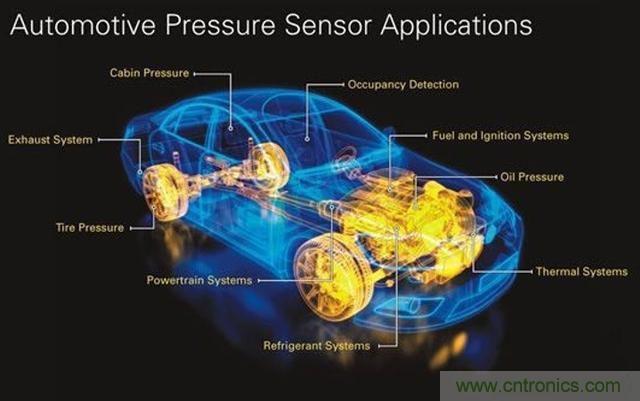
压力传感器在汽车上的应用
如今,MAP和BAP传感器的主要设计是源于硅微加工的压阻式压力传感器。它们大多数用于乘用车中,为微机械压力传感器技术在其它新兴汽车产业中的应用奠定了基础,例如废气再循环系统(EGR)中的压力测量、燃油系统中的蒸发排放物泄漏以及燃料喷射系统的压力测量等。
压力传感器元件
采用体微加工技术在硅晶圆上制造压阻式传感器,已成为生产汽车压力传感器的主要技术之一。压阻式绝对压力传感器元件采用体微加工技术在背面形成真空腔,该结构一问世就广受欢迎,成为MAP/BAP应用的必要元件。然而近期,表压和差压结构,以及仅为消除应力增加的背面约束(backside constraint)结构(见图1),目前已进入量产阶段。
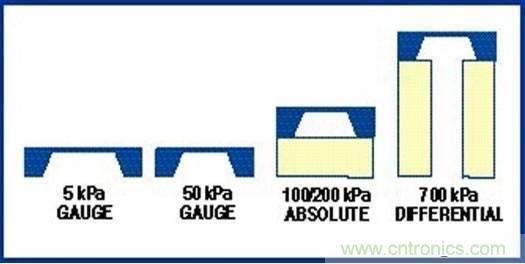
图1:为了满足汽车市场所需的广泛应用,传感器制造商必须能够提供多种传感器元件结构,以分别测量绝对压力、表压或差压的压力范围。
压力传感器信号调理和校准
硅微加工的压力传感器元件在不同生产批次之间以及整个温度范围内的参数变化较大(见图2)。为了让汽车制造商可以获得真正可互换的压力传感器模组,传感器研发人员必须对每个传感器进行单独校准和温度补偿。
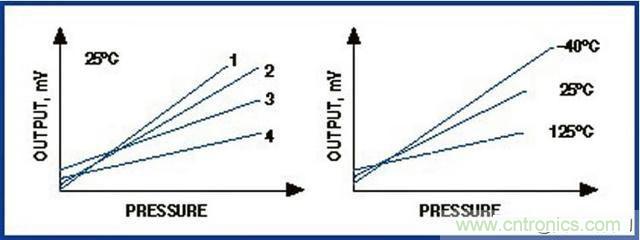
图2:批量处理的硅微加工压阻式传感器元件在圆片与圆片之间、批次与批次之间呈现出器件间的差异。各个压阻元件也随温度产生很大变化。因此,在传感器模组的最终组装过程中,需要对单个封装后的传感器进行单独的修正和校准。
通常的方法是在信号调理电路中运用某种调整(修正)方式。制造和组装工艺以及成品传感器模组的电气性能要求有助于确定信号调理电路的实现方式。该电路的集成技术(如CMOS或Bi-CMOS技术)主要取决于所选的修正技术。
压力传感器模拟信号调理
起初,汽车压阻式压力传感器包含模拟信号调理电路,采用安装在PCB上现成的封装后的Bipolar(双极)IC设计工艺来构建。所有必要的调整都是通过沉积在陶瓷衬底上的厚膜电阻网络的激光修正来完成的,然后再以修正组件的形式嵌入PCB中。后续混合电路技术的进步使得技术人员能够在制造包含印刷厚膜电阻的陶瓷衬底的同时,又能以封装或裸芯形式来安装信号调理IC。技术进步之后,这些传感器模组就变得非常紧凑,其中大部分目前仍在沿用。这种成熟的制造工艺为需求中等尺寸的应用提供了经济高效的传感器模组,其厚膜电阻的稳定性和精度也足以满足客户要求。
然而,由于汽车行业对低成本元件的持续驱动,迫使技术人员研发更高级别的集成技术,最大限度降低压力传感器模组的元件数量和组装成本。随后,通过将模拟有源电路与无源薄膜可修正电阻集成在同一芯片上,制造商大大减小了传感器模组的尺寸,并提高了传感器性能,这主要是因为薄膜电阻器具有优异的稳定性。此集成技术开创了双芯片解决方案,一颗芯片是传感元件,另一颗芯片是薄膜电阻IC。而单片(单芯片)解决方案是将传感元件、有源电路和薄膜电阻集成在同一颗硅芯片上,并适用于大批量生产。
所有上述信号调理电路本质上都是模拟的,并假设激光修正是连续的。
压力传感器离散模拟修正
压阻式压力传感器的第二种信号调理:离散模拟修正,是基于离散而非连续的调整。在这种情况下,可以通过熔化电阻丝,以使电阻或电流值达到期望值。传感器信号的处理仍然保持模拟形态,但是校准和修正是通过离散步骤完成的。这可能会对传感器的精度、分辨率和权限范围有所限制。离散模拟信号调理方法可以进一步扩展,因为调整水平可以存储在非易失性存储器(nonvolatile memory,NVM)中,并以CMOS技术来实现。用离散模拟方法制造的压阻式压力传感器通过混合技术采用了两颗芯片。一颗芯片是将校准系数存储在EPROM(Erasable Programmable Read Only Memory,可擦除可编程只读存储器)中并以CMOS技术来实现;另一颗芯片包括传感元件和放大器,以Bipolar技术来实现。
压力传感器数字解决方案
压阻式压力传感器的信号也可以使用数字信号处理(Digital Signal Processing,DSP)进行调节。通过该方法,压力和温度信号被数字化,然后作为DSP算法的输入。使用算术运算实现校准和温度补偿,之后再将数字信号转换回模拟域。
数字解决方案需要一些内存,因此CMOS技术最适合。虽然汽车制造商们已对此解决方案考虑了很多年,然而,真正实现需要多颗芯片,并且相对较高的成本使其并不适合汽车应用。随着更加先进和高度集成的CMOS工艺和微控制器/DSP技术的发展,此解决方案将会变得越来越普遍。关于用于此目的的标准微处理器设计的芯片大小和电路成本是否会与灵活性较低(但尺寸较小且成本较低)的可定制执行特定传感器校准功能的专用DSP设计相竞争,仍然存在争议。
照片1中所示的集成式压力传感器使用定制DSP和NVM来校准和温度补偿一系列压力传感器元件,适用于各种汽车应用。
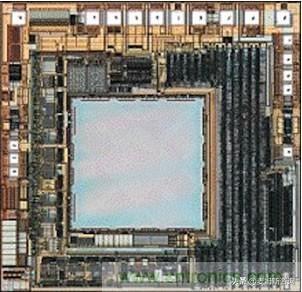
照片1:此单片压力传感器使用定制DSP和NVM来校准和温度补偿片上压阻式压力和温度传感元件。数字信号处理方案还可为客户特定功能提供编程设计。
该可编程信号调理引擎使用校准算法在数字域中运行,该算法解决了超出大多数模拟信号调理方法领域的高阶效应。单片传感器可提供增强特征,这些特征通常在芯片外(或者根本不在芯片上)用传统的模拟信号调理解决方案(使用激光或电学修正)来实现。专门开发的数字通信接口能够在模组完全组装和封装后,通过连接器引脚校准各个传感器模组。取消修正后处理,在制造流程完成时将校准和模组定制作为生产线最终测试的组成部分来执行。压力传感器元件可在亚微米混合信号CMOS晶圆制造过程中被一同处理,而且可以扩展到各种汽车压力传感应用中。数字和模拟传感器输出均适用。
压力传感器制造和组装注意事项
压力传感器模组组装工艺在制造商决定使用哪种修正和校准方法中扮演重要角色,因此也会影响电路设计。激光修正方法需要在组装过程中的某个中间点对模组进行光接入,以执行校准。该步骤通常涉及温度和压力的应用,因此需要对复杂的生产夹具进行仔细维护和校准。由于目前所有量产汽车压力传感器设计都需要某些特定的校准,以确保在客户层面的可互换性,因此修正成为对制造成本和生产率产生重大影响的关键步骤。对于单片和薄膜修正设计来说尤其如此,其中涉及到的微型尺寸和更高精度使模组组装变得更具有挑战性。
此外,后修正(post-trim)的制造操作步骤可能会在模组进行最终测试之前出现输出偏移,因此在最终测试时,该操作则可能会引发参数不合格。考虑到这些因素,制造商仍在继续寻求电气修正方法,使成品模组能够以最终形式进行测试和修正。
汽车硅压阻式压力传感器的集成发展遵循IC行业的总体趋势(见图3)。
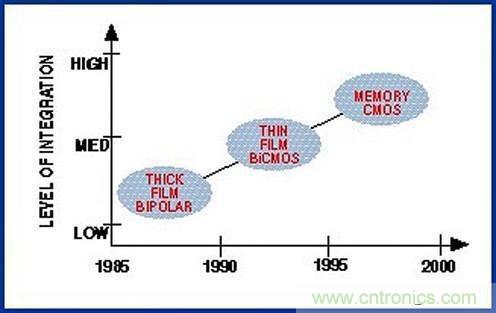
图3:更高级别的传感器集成和校准技术与IC工艺技术的发展趋势同步。
表1总结了一些用于校准、补偿、修正和集成硅微加工压阻式压力传感器的不同方法。
表1:压阻式压力传感器的信号调理和修正方法
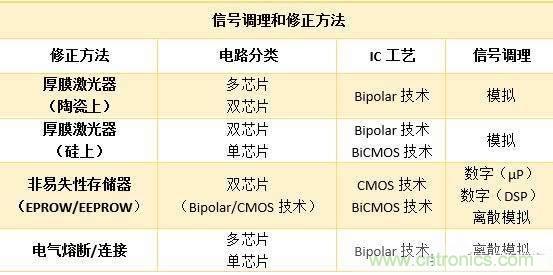
传感器的电学要求
除了基本的参数精度之外,汽车传感器还必须满足其它操作环境和系统要求。表2节选了部分必须要考虑的因素。
表2:传感器的电学要求
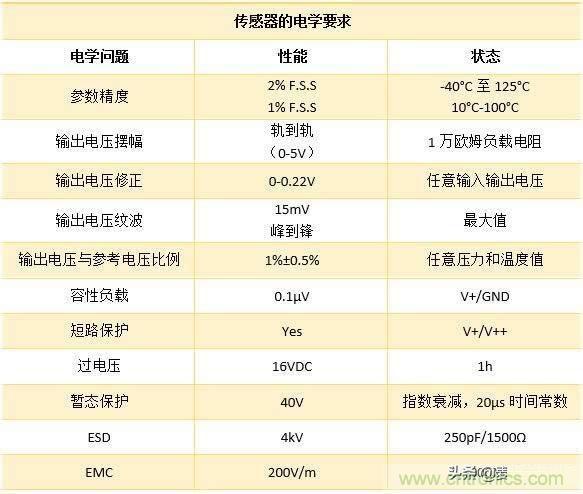
有些因素非常具有挑战性,往往会成为重要的成本驱动因素。在设计过程中它们可以很容易地将原本简单的信号调理电路复杂化。电磁兼容性(EMC)等细节也会影响封装设计和模组组装过程。例如,EMC缺乏足够的电气解决方案就意味着可能需要额外的组件和屏蔽来进行保护。
封装:汽车压力传感器设计的封装组件至关重要,原因有三:
1. 成本
2. 尺寸
3. 恶劣环境下的稳定性
使用微机械加工器件的封装和组装产成本通常超过器件本身,因此,如果想要这样的产品在市场上取得成功,成本则是重要的考虑因素。
传感器元件封装
传感器元件的安装和封装必须满足两个互相矛盾的要求:即为了进行测量,传感器必须与压力传感介质紧密接触,同时还能抵抗介质的不利影响,例如电气互连引起的腐蚀或可能导致传感器输出偏移的应力。这两项要求对材料工程师开发出定制的聚合物密封剂和芯片粘接材料来安装和钝化传感器元件提出了严峻的挑战。
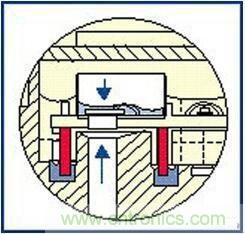
图4:定制聚合物密封剂和芯片粘接材料、详细的结构建模和独特的组装工艺是构建耐介质影响的传感器模组所必需的。图示为安装在燃油箱中的传感器模组中的蒸发排放传感器元件。
基板和芯片粘接材料的选择因制造商而异,但它们在恶劣环境中都必须足够稳定,以防止极低压、高应力敏感元件的长期输出漂移。用于测量燃料喷射压力的传感器也出现过类似的情况:长期暴露在液体燃料和高压下,需要小心选择合适的材料和创建几何结构,以提供稳定可靠的传感器。设计这些传感配置涉及大量的结构分析、机械应力测试和介质暴露测试等。
许多制造商青睐的另一种元件封装技术包括带有电气真空穿通密封件(electrical feedthrough)的金属集管和背面压力接入端口。这种组装方法可以使排放气体密封在密封罐中或者直接排放到大气中,以提供表压测量。此技术的成本往往比背面压力封装更高,在背面压力封装中,元件只需直接安装到有信号调理电子器件的基板上。然而,这是电子行业众所周知的稳健方法,而且使用单芯片集成传感器的信号调理结构可使成本损失最小化。它不需要再开发必须承受测量介质的定制密封剂。
传感器模组封装
传感器模组封装最普遍的方法是嵌入包含引线框的模制塑料外壳,该引线框可为汽车线束连接器提供接口。金属铸造外壳很久之前就被使用了,有些目前仍在生产中,但应用已经很少了。塑料制模和冲压引线框封装技术已经被广泛开发并应用于各种汽车电子模块中,且已适应于在引擎盖下使用的压力传感器,以提供防风雨、环境鲁棒性强的模组。表3列出了测试这些模组及其内置元件以确保车辆使用寿命超过10年或超过10万英里的条件示例。
表3:汽车可靠性要求
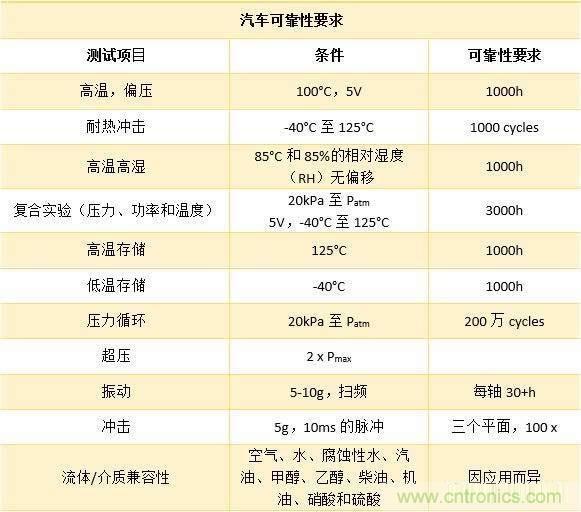
经过多次环境测试,汽车压力传感器通常都可以将其稳定性保持在0.1%——0.3% F.S.S的范围内。在长期而严苛的测试中,例如涉及测试条件组合的测试,或者试图诱发故障的测试,这些传感器仍然可以将稳定性保持在1% F.S.S。
目前有两种基本方法可将传感器元件和电子元件组装在塑料模块内。其中一种方法是先使用基板来组装元件,然后再将基板嵌入并附接到壳体和引线框上。这种技术有助于开发多芯片结构,特别是那些需要额外无源元件来实现过压或EMC保护的结构。需要多个密封件来确保精确的压力测量,同时仍然保持模块的完整性,以避免外部污染或泄漏到外壳上。
目前已经有一些制造商推出了直接安装在外壳上的传感器和信号调理芯片模组,从而可消除使用单独基板的成本(见图5)。这对于高度集成的传感器设计尤其有利,例如需要很少或完全不需要额外无源元件的单片传感器。
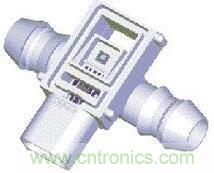
图5:直接安装在模组上的单片压力传感器简化了制造过程,并通过消除使用单独基板或中间芯片级传感器元件封装的需求,提高了现场可靠度测试。
当然,封装的尺寸受到其封装元器件大小的限制,随着传感器和电子器件集成水平的提高,封装尺寸也会变得越来越小。照片2展示了MAP传感器封装尺寸的演变过程,几乎已经达到现有技术下最小的几何尺寸。这归功于汽车制造商对指定的连接器尺寸、压力端口和安装方案的限制。
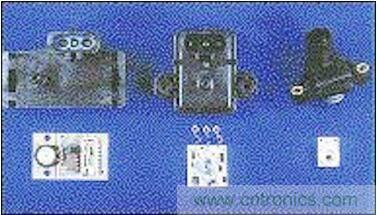
照片2:最成熟的汽车压力传感器应用——MAP传感器的结构已经从PCB组装的分立元件发展到更简单的带有厚膜电阻的混合基板。使用片上薄膜电阻器可以进一步缩小混合电路的尺寸。
商业考虑因素
汽车微机械压力传感器商业开发中的关键考虑因素之一是需要大批量应用驱动(例如MAP传感器),其可提供广泛适用于其它压力传感器产品的基础技术。然后,可以利用传感器元件设计技术、工艺能力和制造资本的安装基础来提供学习曲线效应,从而有利于并加速新应用产品的引进和增长。产品驱动的市场规模需要有足够大的单位数量、绝对金额和利润率,从而来证明进入市场所需的资源和投资水平是合理的。
微机械加工器件可能是高附加值产品的关键赋能技术,这些产品对子系统制造商具有重要的战略意义。例如用于发动机控制的MAP传感器、用于气囊系统的加速度计以及用于车辆动力学系统的惯性传感器等。微机械加工器件可以创造一种“技术非线性”,为供应商提供产品开发能力,使其能够区别于其竞争对手。各种级别的产品集成,例如具有多个传感器的模组,或与执行器和控制功能相结合的传感器,同时也能够与汽车制造商的子系统采购趋势保持一致。
从汽车压力传感器技术的发展演进来看,显然还需要更多技术和能力来生产成功的商业化产品。如机械封装方面的专业知识、材料科学、电路和系统设计、集成电路设计、大批量修正、测量和生产组织,以及满足终端用户系统需求的应用工程都是有助于传感器制造商成功的重要因素。
推荐阅读: