【导读】从IGBT供应商方面来看,究竟该如何实现上述目标呢?这需要站在IGBT器件本身的角度,尤其是IGBT芯片领域来审视。为了实现更高的性价比,IGBT芯片需要有更低的损耗,更高的驱动效率,以及更低的温升,如此才能大幅助力芯片生产商减少芯片面积,提高晶圆尺寸,进而降低成本、提高能效。
从IGBT供应商方面来看,究竟该如何实现上述目标呢?这需要站在IGBT器件本身的角度,尤其是IGBT芯片领域来审视。为了实现更高的性价比,IGBT芯片需要有更低的损耗,更高的驱动效率,以及更低的温升,如此才能大幅助力芯片生产商减少芯片面积,提高晶圆尺寸,进而降低成本、提高能效。
对此,吴海平认为:“一方面,可以对IGBT芯片的电流密度做出提升,例如欧洲一家供应商之前推出的750V的EDT2产品,相比过去650V的IGBT3产品,电流密度提升10%左右的情况下,模块的性能有了超出10%以上的提升,饱和电压也从原来的1.55V降低到了1.15V,这对整车的能耗降低有了很大贡献。”
其次,还需要减少短路耐受时间,“因为短路耐量这个参数如果不好的话,一旦发生上下桥直通时IGBT会容易烧毁,所以IGBT都会有短路耐受时间的要求。这就需要我们通过在系统上做更好的保护,减少对短路耐量的需求,保证损耗的参数能够降得更低,从而使整车效率能够提升。比亚迪在去年推出的IGBT 4.0技术,当时对标的就是欧洲竞争对手的IGBT 4产品,在综合损耗上还要略低20%。”
最后,还有功能集成化,吴海平举例到:“一般来说,IGBT在使用时都需要做过温保护,目前过温保护大部分都使用的是模块里面集成的热敏电阻,通过这个热敏电阻检测芯片是否过温。但热敏电阻离芯片有一定距离,不能实时反应芯片实际温度。而且,热敏电阻还有一定的热容,和芯片之间的结温有很大的差异。在一些功率模块上,热敏电阻的温度和芯片结温存在高达60℃的温差,好一点的有30℃的温差。如果保护芯片在150℃以下,NTC到了80℃就要保护了,导致要留很大的余量。”
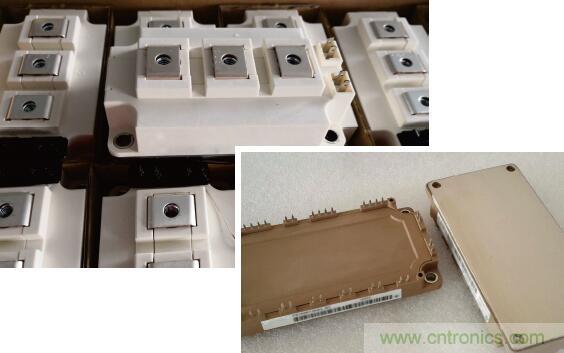
所以,如今对于IGBT芯片的保护方式就是将温度检测直接放在芯片端,“比如在芯片中间嵌入一个温度传感器,实际原理就是利用二极管的VF随着温度的线性变化,只需要检测二极管的VF之后便可很清楚的知道芯片当时的温度,非常及时准确。而且,为了避免IGBT芯片的误保护,需要在内部引入具有电流检测的单元,实际上就是与过去的主IGBT并联一个更小的IGBT,对IGBT做过流保护。正常的IGBT工作在300A,可以把保护点设置在500A来进行及时保护,保护比较快,从而能进一步减少芯片对短路耐量的依赖,降低VCEsat。”吴海平进一步补充到。
当然,除了芯片以外,为了持续降低IGBT成本,晶圆尺寸也是另一大关键。吴海平表示:“虽然功率器件对晶圆尺寸依赖不是很大,因为芯片内的线条尺寸都比较大。但近年来,随着各种新概念的出现,比如很多国际大厂推出的新一代的IGBT,都开始把尺寸做得更小。”这从生产商的角度来看,也就需要更好的产线,降低单颗IGBT芯片的量产成本。
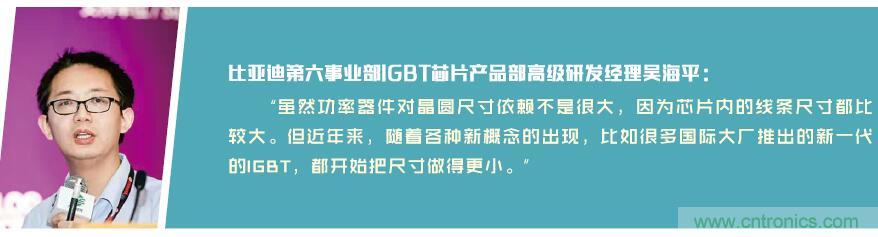
毕竟,更大的晶圆有利于提高生产效率,早期市场上流行的都是6寸,但如今8寸已逐渐成为市场主流。据国际半导体产业协会(SEMI)日前发布的报告中披露,自2018年7月以来,全球增加了7个200mm新厂房。且2019年到2022年间,全球预计共将有16个厂房或产线,其中14个为批量Fab厂,带动全球八英寸产能的直接提升,预估2022年,全球的200mm晶圆制造厂的总产能将达到650万片晶圆/月。
从今年国内市场的一系列动向,也能发现各本土企业都开始蠢蠢欲动,为争夺8寸IGBT芯片市场整军备战。比如今年3月,代工大厂富士康就在济南投建了8寸功率半导体晶圆产线,主要以8寸晶圆厂功率半导体器件(主要生产MOSFET、CoolMos、IGBT器件)和6寸晶圆厂碳化硅器件的研发、生产为主;4月,天毅半导体在绍兴的IGBT项目也签订了落户框架协议,投资额为5亿元,主攻IGBT、MOSFE模块等的设计、研发与生产制造;8月,台湾合劲半导体在东海经济开发区投资兴建 了“再生晶圆和IGBT”项目,总投资7500万美元,达产后可年产8-12寸再生晶圆150万片的规模;同在8月,合肥中恒微半导体IGBT模块首期投产仪式也正式落成,一期产能建成后,可实现30万只IGBT模块的生产,二期规划2020年开工建设,全部建成后,年产达100万只IGBT模块。
这样类似的项目还有很多,这也说明8寸IGBT领域,如今已有越来越多的企业正在扩充产线、奋力角逐,但这并不意味着IGBT的降成本之路正式走上了阳光大道。有受访者指出:“因为一方面,IGBT产业有着很明显的规模经济的特征,虽有了产线这个基础,但厂商如果无法在短期内提升真实产量的话,将承受成本高于原有老牌大厂的劣势,面临巨大的财务压力。而且更有可能会激起诸如英飞凌、安森美等老牌大厂们的反制,进而导致竞争压力急剧增大。”
更何况,除一些闻名遐迩的国外大厂外,现阶段国内真正有能力加工IGBT的产线(不管6英寸还是8英寸)都比较少,能为IC设计公司提供代工服务的产线则相对更少,比如华虹宏力、苏州和舰等几家企业,是当前国内为数不多的几家可用8英寸晶圆产线为客户代工的厂商。毕竟,IGBT作为电动汽车核“芯”中的核心,非常考验厂商的晶圆制造的能力和经验,只有具备深厚的技术底蕴和强大的创新能力,并持续进行技术积累,才能在行业里立足。
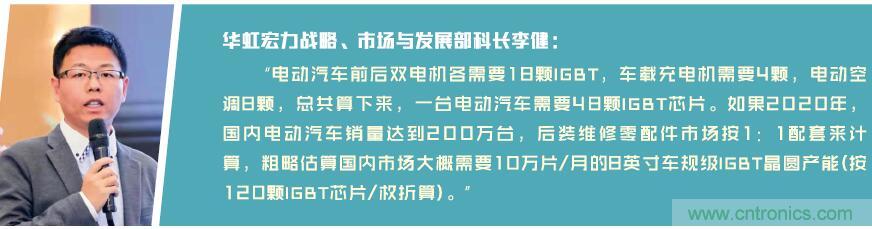
就以IGBT芯片背面加工工艺为例,现阶段国内真正攻克这一技术难关的企业屈指可数,李健曾指出:“IGBT晶圆的背面加工需要很多特殊的工艺制程,以最简单的薄片工艺来说,一般正常的8英寸晶圆厚700多微米,减薄后需要达到60微米甚至更薄,就像纸一样,不采用特殊设备会弯曲而无法进行后续加工。如今,华虹宏力已拥有背面薄片、背面高能离子注入、背面激光退火以及背面金属化等一整套完整的FS IGBT的背面加工处理能力,使得客户产品能够比肩业界主流的国际IDM产品。”而对于更多的新晋厂商来说,能否在工艺层面上达到如这些老牌大厂们那般水准可想而知。
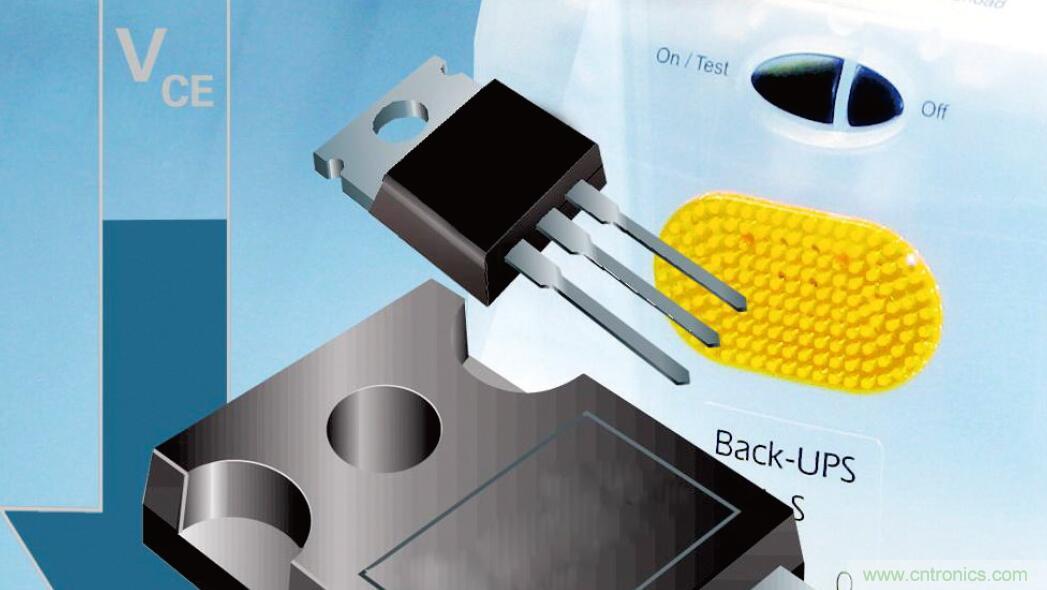
因此,宏观层面上,即便是国内如今已涌现出越来越多的本土企业竞相发力8寸IGBT市场,但从影响力上来看,编者认为仍旧如杯水车薪。因为当前,无论国内外品牌新能源汽车所采用的IGBT芯片和模块,绝大多数的市场份额仍被国外诸如德国英飞凌、日本三菱、富士电机、美国安森美等美日欧系厂商占据,国内厂商从份额上看影响力着实有限,市场主导权仍由国际大厂紧紧攥于掌中。由此可见,国内新能源车厂想要摆脱因补贴减弱和销量不振造成的增长乏力难题,短期内仍困难重重。
但长期来看,随着国内越来越多如比亚迪这般在全球IGBT技术和市场方面都有相当积累和影响力的企业出现,加之国内8英寸产能的持续扩张,未来有望逐渐形成与国际大厂分庭抗礼之势。不过,这还需要更多本土车企的开放支持,否则,IGBT市场乃至整个新能源汽车系统零部件成本的掌控权和市场的定价权,仍旧只能被紧紧攥于他手。