【导读】通过推出DCM 1000X,丹佛斯扩展了DCM 1000技术平台,用于混合动力电动汽车和电池电动汽车的牵引应用。DCM 1000X采用1200V半导体,采用Si或SiC。具有1200V阻断电压的SiC基DCM 1000X模块专为使用高达950V的直流母线,额定电流范围为200A-800A的传动系设计。1200V平台满足所有常用的绝缘要求,例如LV123,IEC 60664-1或950V DC链路电压的其他安全裕度。
全球变暖,污染和国际碳排放目标启动了减少汽车排放的过程。汽车行业正在通过增加车辆电气化来推动提高燃油效率和减少排放。全球对BHEV,BEV车辆和新动力传动系统设计的需求不断增加,这促使汽车制造商评估其当前和未来设计中适用的电力电子技术的构成。汽车制造商不断寻求提高整体性能:更高的转换效率,更低的成本,更轻的重量和更高的功率密度。提高能源效率可降低行驶一定距离所需的能源消耗和电池容量。
与硅(Si)IGBT或MOSFET相比,碳化硅(SiC)MOSFET具有多个优点,即更快的开关能力,减少电机的损耗并改善传动系的声学特性。通过增加开关频率,可以实现更正弦的电动机电流,从而减少电动机损耗,降低导通状态和开关损耗,并增加导热率和介电强度。有助于提高功率密度并显着降低逆变器的重量和体积。
需要从系统级别评估SiC器件的全部功能,因为这些可能会给传动系中的其他组件带来挑战。例如,利用没有输出滤波器的高开关频率会导致高电压斜率(dV / dt),从而导致电机绝缘击穿。此外,更高的开关频率会导致不希望的电容耦合和EMI问题。
认识到高SiC器件成本是反对SiC技术采用的最明显的论据之一。SiC芯片组的价格目前是Si芯片组的几倍。随着先前半导体技术的发展,假设SiC芯片组价格将随着采用率的提高而降低,从而推动更高的晶圆厂生产能力和技术进步增加晶圆直径。
混合动力电动汽车(HEV),插电式混合动力电动汽车(PHEV)和电池电动汽车(BEV)都包含几个关键系统,这些系统将受益于碳化硅动力装置,从而提高电动汽车的能效和性能。
DCM 1000X
通过推出DCM 1000X,丹佛斯扩展了DCM 1000技术平台,用于混合动力电动汽车和电池电动汽车的牵引应用。DCM 1000X采用1200V半导体,采用Si或SiC。具有1200V阻断电压的SiC基DCM 1000X模块专为使用高达950V的直流母线,额定电流范围为200A-800A的传动系设计。1200V平台满足所有常用的绝缘要求,例如LV123,IEC 60664-1或950V DC链路电压的其他安全裕度。
与DCM 1000(750V)一样,DCM 1000X可在最恶劣的条件下运行; 高温循环(高达135K),高湿度,机械冲击和振动。使用功率模块的特定传递模具封装材料(环氧树脂 - 葡萄干涂层)来解决冲击和振动要求,如图1所示。
为了达到最大功率循环性能和使用寿命,DCM 1000X平台模块使用Danfoss Bond Buffer技术(DBB),DCM 1000也是如此.DBB可以在更高的结温下运行。与任何其他标准键合和连接技术相比,烧结半导体到基板结合DBB和铜线键合提供更高的功率和温度循环能力,寿命高达15倍。
图1还显示DCM 1000X采用直接液体冷却技术ShowerPower 3D,有助于实现出色的散热性能。与其他液体冷却技术(例如针翅式冷却器)相比,SP3D概念具有多种优势。
并联冷却原理消除了与串联冷却针翅概念相关的温度梯度。它还允许定制冷却通道,以便将冷却集中在局部热点; 由于“阴影”效应(1),针翅概念不可能实现的功能。
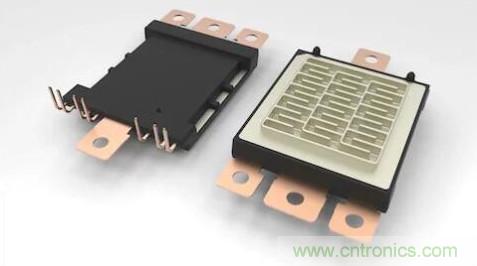
图1. DCM 1000X
DCM 1000X经过精心设计和优化,可充分利用芯片独立性。丹佛斯Silicon Power可以提供基于不同半导体的DCM 1000X设计,从而确保具有吸引力的成本基础,优化设计和安全供应。
电气性能DCM 1000X
DCM 1000X满足电动汽车市场对450V至950V的近乎双倍直流链路电压的要求,实现更高的输出功率和更快的充电能力。通过使用Si IGBT或SiC MOSFET的1200V半导体,可以实现高效的200kW逆变器设计或更高。通过更高的直流母线电压,相电流可降低50%,在较低的直流母线电压下保持与逆变器相同的输出功率,并实现不到10分钟的快速充电时间。由于这种关系是非线性的,因此与具有相同占位面积的经典650V / 750V电源模块相比,使用DCM 1000X封装中的1200V IGBT可以实现更高的输出功率。
如上所述,SiC MOSFET的优势在于MOSFET的导通状态和低开关损耗,因此可提供最佳的部分负载优势,因此如果逆变器使用更高的开关频率,则可获得更大的整体效益。
图2显示了1200V Si IGBT / FWD(1000mm²硅)和SiC MOSFET(400mm²碳化硅,无外部二极管)的相电流之间的比较。假设两个逆变器的冷却剂边界条件,10升/分钟最小流量和65℃最大冷却剂温度保持不变。
典型的汽车逆变器设计规则规定175°C额定器件的最大工作IGBT结温为165°C,而对于SiC MOSFET,额定SOA为200°C时,最大设计工作结温为190°C。请注意,这些温度只能通过使用DBB®来实现,包括低于最大工作芯片结温的安全裕度。
此外,如上所述,ShowerPower 3D冷却器可在冷却剂条件下实现0,1K / W 的无法达到的R th ; 对于200mm²的总SiC MOSFET面积和每个开关300mm²的总IGBT面积,由于芯片尺寸的不同,这是正确的。
这个Rth意味着,对于SiC结温为190°C且温度差值为125K,模块总损耗限制在2.5kW,DCM 1000X在峰值负载下能够耗散超过625W /cm²的能力。上述冷却条件(IGBT模块损耗为2kW,IGBT功能耗散为325W /cm²)。
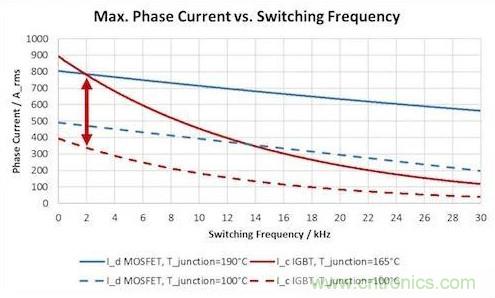
图2.恒定结温时的最大相电流与开关频率(10K裕量至最大允许结温175°C和200°C),850VD
在图2中,SiC MOSFET仅在开关频率上显示出最大相电流的轻微下降,证明了SiC在高开关频率下的巨大优势。换句话说,在低开关频率下实现最高的IGBT性能而不降低额定值。因此,使用SiC MOSFET可以实现相同输出功率和合理开关频率的更高逆变器效率。只有通过增加Si面积才能达到比较效率,但缺点是空间增加和系统成本增加。此外,对于图2 中T 结 = 100°C所示的部分负载,Si和SiC之间的差异变得更加严重。
汽车1200V IGBT牵引功率模块仍将具有成本吸引力。深入研究DCM 1000X的性能,将DC链路电压加倍并将电流降低不到50%,这表明SiC的成本驱动因素是1200V IGBT技术的性能,已经可以实现475V的性能提升在使用SiC MOSFET之前,要达到950V DC链路电压。
推荐阅读: